Different alloys prepared from nickel differ in terms of grade, composition, shape and features, and characteristics. So, you must know some important properties of these alloys to learn about their specific uses. Nickel alloys are alloys in which nickel is the primary constituent element.
Between nickel and copper, there is complete solubility in solid form. Because of the wide solubility ranges between iron, chromium, and nickel, a large number of alloy combinations are conceivable.
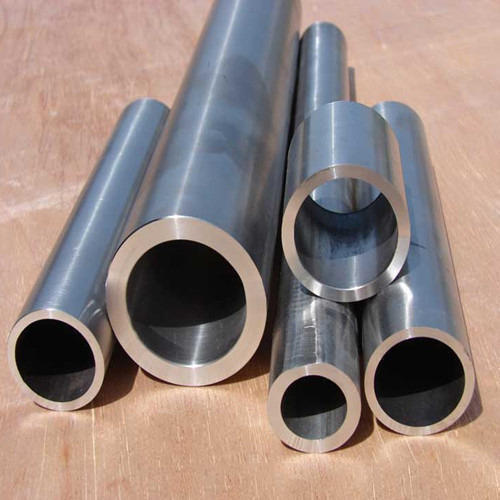
Introduction to Nickel
Nickel is a versatile element used for products as widely varied as tableware and handcuffs. Nickel coins contain nickel metal, of course. Nickel electroplating provides a protective coating that is also attractive, with a shiny finish that appeals to manufacturers of decorative items like vanity faucets, garden fountains, stainless steel serving trays, knick-knacks, and Christmas decorations. Pure nickel is used less often than nickel alloys, and it provides benefits like greater strength or greater heat resistance than nickel alone. With a focus on the ever-evolving demands of customers, Nickel Alloy Casting Manufacturer makes and supplies a wide range of exceptionally designed Nickel Casting.
The process of making Nickel Alloys
Nickel may be alloyed with a wide range of other metals in addition to chrome, iron, molybdenum, and copper. It enables the development of a diverse range of alloys that exhibit excellent corrosion and high-temperature scaling resistance, extraordinary high-temperature strength, and other unique characteristics like shape memory and a low coefficient of expansion.
Start with the purest raw materials available to ensure that the alloy has the chemical composition needed to manufacture Nickel Alloys. It is essential to have a suitable chemical composition for various alloys to have consistent and desired characteristics. With the use of cutting-edge technology, the alloys are then melted, hot-rolled, and processed to their final shapes and sizes.
The manufacturer continuously monitors all processes at each stage, and statistical process control techniques are used to guarantee that the final products are of the highest possible quality. They establish the method for manufacturing each alloy after a thorough exercise that incorporates ideas such as Failure Mode Effect Analysis (FEMA) and Design of Experiments (DOE).
Also read: What Is Casting Nickels Out Of Lead Meaning?
Several steps in Nickel Alloys making process
Several of the stages are outlined in more detail below.
- Using Electric arc, air induction, vacuum induction melting, and mechanical alloying are all methods of melting metals.
- Forging, hot rolling, and extrusion are examples of hot working.
- Cold working techniques include rolling, drawing, and pilgering.
- Acid pickling, vacuum refining, vacuum arc, and electroslag remelting are some of the processes used.
- Tensile testing, hardness testing, elastic testing, microstructure inspection, purity assaying, mechanical testing, and dimension testing are all examples of quality control procedures.
Nickalite alloys are widely utilized for a variety of applications because of their corrosion resistance, high-temperature strength, and unique magnetic and thermal expansion characteristics. Producing extremely cost-effective alloy investment castings requires the use of cutting-edge methods and technology. Nickel Alloy Casting manufacturers use the highest-quality raw materials to fulfill the requirements of national and international quality standards.
Major alloy types used:
- Iron-Nickel-Chromium alloys
- Stainless Steels
- Copper-Nickel alloys and Nickel-Copper alloys
- Nickel-Chromium and Nickel-Chromium-Iron alloys
- Low Expansion Alloys
- Magnetic Alloys
Also read: How Does A Ball Valve Work?